В КБГУ получили материалы, способные заменить металлы
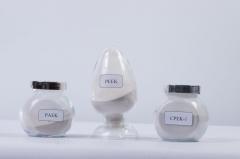
Ученые Кабардино-Балкарского государственного университета им. Х. М. Бербекова (КБГУ) совместно с российскими исследовательскими коллективами представили новые полимерные материалы, которые могут стать полноценной альтернативой металлам в ряде высокотехнологичных отраслей — от медицины до авиастроения. Разработка отличается уникальным сочетанием свойств: материалы работают в экстремальных температурных диапазонах от –100 до +300 °C, при этом они существенно легче традиционных металлов — на 70% легче титана, на 50% легче алюминия и на 80% легче стали.
Современная промышленность, особенно авиационная и автомобильная, остро нуждается в материалах, которые позволят снизить массу конструкций без потери механической прочности и термостойкости. Каждый лишний килограмм в самолете или автомобиле приводит к увеличению расхода топлива и выбросов парниковых газов. Однако большинство существующих полимеров уступают металлам по этим показателям, что ограничивает их применение в ответственных узлах и деталях.
Новые полимеры КБГУ решают сразу несколько задач:
- Экстремальная термостойкость: сохраняют свойства при температурах от –100 до +300 °C.
- Снижение веса: на 70% легче титана, на 50% легче алюминия и на 80% легче стали.
- Экологичность: производство не образует отходов, материалы пригодны для вторичной переработки.
- Высокая прочность: позволяют создавать конструкции, не уступающие металлическим аналогам.
- Экономическая эффективность: замена 15 000 металлических зажимов в одном самолете на полимерные аналоги позволяет сэкономить более 2 млн рублей на топливе и снизить выбросы CO₂ на 80 тонн в год.
«Наши материалы могут заменить металлы в различных отраслях, существенно снижая вес изделий. Это открывает новые возможности для производства деталей, которые невозможно получить традиционными методами», — отмечает проректор по научно-исследовательской работе КБГУ Светлана Хаширова.
Ключевым элементом разработки стала адаптация технологии порошкового литья (PIM), ранее применявшейся только для металлов и керамики, к высокомолекулярным полимерным порошкам. Этот метод позволяет использовать сложные в переработке материалы, такие как полиэфиркетоны (PEEK), полиэфирэфиркетоны (PEEK), полисульфоны и полифениленсульфоны (PPSU), которые уже доказали свою эффективность в авиации и медицине.
Преимущества метода:
- Возможность изготовления изделий сложной геометрии.
- Исключение отходов производства.
- Сокращение времени изготовления деталей.
- Возможность переработки сверхвысокомолекулярных порошков, ранее недоступных для традиционных методов (экструзии, литья под давлением).
Старший научный сотрудник Центра прогрессивных материалов и аддитивных технологий КБГУ Азамат Слонов подчеркивает, что оптимизация условий спекания позволила создавать детали сложной формы с высокой точностью, что невозможно при классических технологиях.
Особое значение новые полимеры имеют для медицины. Благодаря прочности и биосовместимости они подходят для многократной стерилизации и создания легких хирургических инструментов, что облегчает работу врачей при длительных операциях. В ближайших планах ученых — вывод на рынок 10 новых медицинских марок полимеров, которые ранее не производились в России.
«Наши материалы технологичны, мы можем делать их такими, чтобы они перерабатывались любым доступным методом, в том числе 3D-печатью. Мы можем изготовить имплантат непосредственно под определенную травму и очень быстро. Материал полностью безопасен для контакта с организмом человека», — рассказала Светлана Хаширова.
Экологическая составляющая разработки заключается не только в снижении выбросов при эксплуатации изделий, но и в самом процессе производства: технология исключает образование отходов и позволяет повторно использовать материалы. В планах КБГУ — масштабирование производства, создание новых композитов и расширение ассортимента для различных отраслей, включая автомобилестроение и промышленный дизайн.
Исследования ведутся совместно с Институтом нефтехимического синтеза им. А. В. Топчиева РАН и реализуются при поддержке Российского научного фонда. Уже заключены договоры с промышленными партнерами на разработку новых компаундов для различных отраслей.